Расчетные задания глава 9
ПРИМЕР РАСЧЕТА БАРАБАННОЙ СУШИЛКИ
Исходные данные
Производительность по высушенному материалу GK=3,3 т/ч
(сульфат аммония)
Начальная и конечная влажности материала uH=2,0 и uK= 0,2%
(на общую массу)
Среднее значение насыпной плотности материала Рнас=820кг/м2
Удельная теплоемкость сульфата аммония сТ=1,47 кДж/(кг·К)
Начальная и конечная температуры материала uH=20 и uK= 60°С
Доля уноса мелких фракций материала 6%
Температуры воздуха на входе и на выходе из сушилки t1=120 и t2= 60 °С
Температура и относительная влажность атмосферного воздуха t0=20 и ф0= 60%
Барометрическое давление П=745 мм.рт.ст
Коэффициент заполнений барабана материалом и насадкой фМ=20 и фЦ= 5%
Тепловые потери составляют 10 % от теплоты испарения и нагрева материала.
Дисперсный, мелкокристаллический сульфат аммония с широким гранулометрическим составом может быть высушен в барабанной сушилке, представляющей горизонтальный, слегка наклоненный вращающийся полый цилиндр, в котором дисперсный материал, заполняя нижнюю часть (15-35 %) барабана в виде плотного слоя, одновременно пересыпается сверху вниз за счет подъема части сыпучего материала насадкой, вращающейся вместе с барабаном. Термочувствительный сульфат аммония не позволяет использовать значение температуры сушильного агента выше t1=120?С, что делает целесообразным использование воздуха, подогреваемого греющим паром, а не топочных газов. Высушивание до низкого значения конечной влажности предпочтительно при прямоточной схеме движения сушильного агента и сушимого дисперсного материала.
Скачать пример расчета барабанной сушилки
(86.85 Кб) скачиваний1150 раз(а)
ПРИМЕР РАСЧЕТА СУШИЛКИ С ПСЕВДООЖИЖЕННЫМ СЛОЕМ
Исходные данные
Производительность по высушенному материалу GK=20т/ч; (хлориду калия)
Влажность материала (на общую массу)
начальная uH=10%
конечная uK= 0,5%
Средний диаметр частиц dmax= 0,5мм
dmin= 0,1мм
Температура исходного материала uK= 20 C
Удельная теплоемкость хлорида калия сM=0,712 кДж/(кг·К)
Плотность хлорида калия рM=2000кг/м3
Параметры атмосферного воздуха t0=20 C и ф0= 65%
Тепловые потери составляют 15 % от расхода теплоты на испарение и на нагрев влажного материала.
Сушка термостойкого хлорида калия может производиться наиболее дешевым теплоносителем - топочными газами, представляющими собой продукты сгорания углеводородных топлив.
Состав топочных газов отличается от состава атмосферного воздуха, используемого в качестве окислителя, лишь заменой части кислорода, пошедшего на окисление углерода и водорода топлива, на соответствующие реакциям окисления диоксид углерода и пары воды; основной же частью топочных газов, кок и воздуха, остается азот (более 70%), Это обстоятельство, с учетом не слишком значительного различия основных теллофизических свойств отдельных компонентов воздуха и продуктов сгорания, дает основание производить приближенные расчеты процессов сушки топочными газами по теплофизическим свойствам атмосферного воздуха.
Выбор конструкции сушильного аппарата и условий процесса сушки производится на основе следующих факторов:
1) высушиваемый материал в сухом состоянии - сыпучий, во влажном - несколько комкующихся;
2) материал выдерживает нагрев до относительна высокой температуры (температура плавления хлорида калин равна 770°С);
3) отношение максимального размера частиц к минимальному размеру dmax/dmin = 0,50/0,10 = 5 не слишком значительное;
4) удалению подлежит в основном поверхностная влага;
5) при сушке солей рекомендуется газораспределительная решетка с диаметром отверстий для прохода сушильного агента dотв=5,0 мм;
0) поскольку высушенный дисперсный продукт предполагается для последующего хранения в течение некоторого времени, то допускается некоторая неравномерность выгружаемого из сушильного аппарата материала по влагосодержанию его отдельных частиц.
Анализ указанных факторов показывает, что следует выбрать однокамерный сушильный аппарат с псевдоожиженным слоем дисперсного сушимого материала и вертикальными стенками (рис. 9.17), а температуру сушильного агента на входе в сушилку (под газораспределительной решеткой) (t1=800?С. Температура сушильного агента на выходе из псевдоожиженного слоя принимается равной t2=125?С, что позволяет исключить конденсацию водяных паров в пылеулавливающей аппаратуре сушильной установки. Для достаточно мелкодисперсного материала при сравнительно низком его конечном влагосодсржании температуру выгружаемого продукта можно принять равной температуре отходящих газов, т. е, uк = 125?С. Высота hсл псевдоожиженного слоя принимается в четыре раза больше высоты hстр зоны действия газовых струй, выходящих из отверстий решетки [9.5]:
Для обеспечения равномерного псевдоожижения по всему круглому сечению аппарата подача комкующейся влажной соли производится разбрасывателем, равномерно распределяющим исходный материал по всей поверхности слоя. Выгрузка продукта из псевдоожиженного слоя производится одновременно с верхнего уровня слоя (для поддержания его постоянной высоты) и из пространства над газораспределительной решеткой (для вывода возможных комков материала).
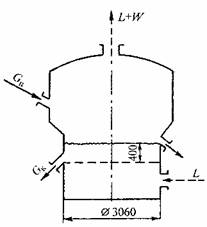
Рис. 9.17. Эскиз аппарата для сушки дисперсного материала в псевдоожиженном слое
Скачать пример расчета сушилки с псевдоожиженным слоем(95.96 Кб) скачиваний1024 раз(а)
ПРИМЕР РАСЧЕТА ВАЛЬЦОВОЙ СУШИЛКИ
Исходные данные
Производительность по влажному пастообразному GK=90 кг/ч
материалу (паста гидрокарбоната натрия)
Начальное и конечное влагосодержание uH=75 и uK= 20%
(на общую массу)
Давление сухого греющего пара рабс=1 кгс/см2
Толщина слоя пасты на поверхности барабана бМ = 1 мм
Толщина чугунной стенки барабана бЧ = 10 мм
Скорость воздуха над слоем материала w = 1,7 м/с
Температура и относительная влажность воздуха t0=4 C и ф0= 40%
Среднее значение коэффициента теплопроводности слоя материала
См=0,80 Вт/(м·К)
Удаление влаги из тонкого слоя влажной пасты происходит в периоде постоянной скорости сушки.
Для сушки пастообразных материалов может использоваться двухвальцовая сушилка непрерывного действия с подачей греющего пара во внутреннее пространство полых вращающихся барабанов к нанесением равномерного тонкого слоя исходной пасты на наружные цилиндрические поверхности, откуда подсохшая паста удаляется ножами (скребками).
Теплопередача в вальцовой сушилке происходит от греющего пара к внутренней поверхности барабана, через чугунную стенку барабана, поперек слоя высушиваемого материала и от наружной поверхности слоя материала к воздуху, причем на последнем этапе перенос теплоты осуществляется парами удаляемой из материала влаги.
Скачать пример расчета вальцовой сушилки(44.28 Кб) скачиваний976 раз(а)